Replace Legacy Logistics Software for a Better Supply Chain
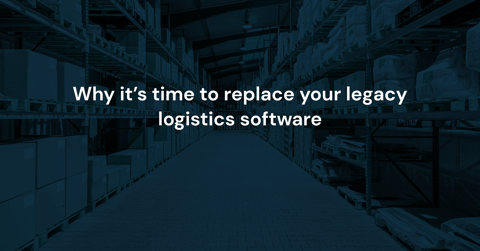
Companies like Amazon couldn’t have made fast, low-cost shipping the industry standard without rethinking the technology they used to power operations. The limitations of incumbent on-premise software were getting in the way of the ability to accurately analyze patterns, shop for rates, optimize packaging and much more.
The most advanced supply chain networks are powered by more advanced, cloud-based platforms that scale on demand, integrate with other key logistics systems, and enable organizations to effectively leverage their data to make smarter decisions through predictive analytics.
In this article, we’ll explore the key differences between traditional on-premise logistics systems and modern cloud-based solutions, and explain why the latter represent the future of shipping technology.
What defines an end-to-end shipping solution?
Before diving into the differences between on-premise and cloud-based logistics platforms, let’s first explore what defines an end-to-end shipping solution. These are software platforms that you can use to navigate every stage of enterprise shipping operations at scale — from making a dependable delivery promise to printing labels to reporting on overall shipping performance.
Here are the specific shipping operations that your platform should support.
Delivery promise
Today’s online shoppers make purchase decisions based on the availability of an EDD before orders are placed, as evidenced by the fact that retailers average a 4% checkout conversion improvement when they make a delivery promise to shoppers (in the context of an enterprise retailer doing $100m in annual sales, this represents a significant chunk of lost revenue).
Ideally, your delivery promise should be based on accurate time-in-transit estimates that are generated using all relevant and available data about your shipping network — we’ll explore this use case in more detail later.
Integration requirement(s): To present accurate, data-driven delivery promises to customers, your platform should integrate with your ecommerce platform/PDP so that you can present EDDs directly within the checkout experience.
Order routing & fulfillment
When it comes to routing and fulfillment, it’s important to have a platform that can support you throughout the many key aspects of this stage — including consolidating orders for shipments, determining the most effective origins, providing real-time visibility into inventory, and helping with routing, packaging, and split reduction. Ideally, your platform will also give you the ability to evaluate carrier eligibility and rates at this earlier stage, which enables you to streamline operations and optimize costs.
Integration requirement(s): At this stage in the shipping lifecycle, the platform you’re using should integrate with your OMS so that you can capture relevant order details like customer information, SKUs/items, and quantities.
Carrier selection & management
Your platform should help you determine the best carrier method based on your defined criteria, whether you’re prioritizing cost optimization, fastest delivery speed, greatest service coverage etc.
In fact, with the necessary integrations and visibility into your network, the right platform should help you increase delivery speed while reducing carrier costs. This means providing a wide range of carrier options, basing time-in-transit estimates on more than just carrier SLAs, and giving you the flexibility and control to make changes quickly.
Integration requirement(s): To support carrier selection, your platform will need to integrate with your WMS to collect information on a shipment’s origin, destination, SKUs and packaging details, and any unique shipment properties/considerations (ex. Lithium-ion batteries).
Track-and-trace
When managing millions of shipments across multiple carriers, tracking shipments from origin to destination can be challenging and time-consuming. If you choose to manage this in-house, the most common options are to either build and maintain multiple carrier API integrations or a solution to consolidate shipments from multiple carriers. Both approaches require investment and coordination from multiple teams, as well as significant engineering resources.
The right end-to-end shipping platform should consolidate shipments and provide real-time updates for key events so that you can manage track and trace more efficiently without a significant investment of engineering resources.
Integration requirement(s): When it comes to track-and-trace, the most significant requirement is integration with various carrier APIs so that your platform can consolidate updates. Ideally, you’ll be able to configure and manage specific webhooks so that you can receive updates about specific events — it’s obviously also a plus if your platform standardizes the structure of these updates.
Reporting and analytics
Lastly, it’s important for a shipping solution to help you measure both the efficiency of specific shipping processes and overall performance. If you choose to invest in this type of platform, it’ll likely be the only technology you have that can provide this level of visibility.
Integration requirement(s): Your shipping platform should integrate with major BI & Analytics platforms like Tableau and Power BI so that you can manage shipping analytics in the same place as the rest of your organization’s reporting. It’s also worth noting that the reports you run are powered by the other logistics integrations that we’ve already explored.
Outcomes your solution should drive
While there are hundreds of use cases that end-to-end shipping platforms can be leveraged for, these overall outcomes should be top of mind:
- Data leverage: The wealth of data generated by your shipping network can help to uncover many opportunities for improvement, if you can properly leverage it. This isn’t possible with disjointed technology and manual processes — you’ll need a comprehensive solution in place to effectively make use of your data.
- Control and flexibility: Ultimately, your shipping platform should give you complete control over shipping operations, and the ability to adapt quickly as your business grows and processes evolve. Strong network management capabilities, integration with other systems, and ease of use are all musts.
- Faster and lower-cost shipping: Yes, you can have both. By providing you with the data leverage you need to identify opportunities and the control it takes to take advantage of them, the right shipping platform should help you improve both shipping performance and your margins.
Why cloud-based logistics software is the future
The market for comprehensive logistics software can largely be divided into on-premise and cloud providers. On-premise platforms (ex. ProShip) have been a staple in the market for over 20 years, and are still relied on by some of the world’s largest retailers. However, in recent years, more enterprises have begun to replace incumbent on-premise technology with more flexible cloud-based solutions, just as they have with other software categories.
In the section, we’ll explain a few reasons why.
Lower, more predictable costs
The most immediate advantage that cloud-based software offers over on-premise is the lack of initial capex associated with hardware and infrastructure. There are also several ongoing costs that come with on-premise software, such as server maintenance, provisioning of additional infrastructure as needs scale, replacements for failing hardware, and energy consumption. These are a non-factor for enterprises that have moved to the cloud.
It’s also worth noting that the Software-as-a-Service (SaaS) billing model is subscription-based, which makes pricing consistent and relatively easy to budget for.
Scalable, interoperable software
The benefits of cloud-based software for scalability extend beyond the direct investment that’s required to support it. It’s also worth considering the significant time savings that your IT team will experience given the relative simplicity of implementation, scale, provisioning of new users etc. that cloud providers offer. In short, your teams have the ability to just focus on making the best use of your logistics software, rather than administering and managing it.
We’ve already explored how critical integrations with the various other logistics tools in your stack are. Cloud solutions offer pre-built APIs for ease of integration across every stage of shipping operations (ex. Your online store, OMS, WMS, BI/Analytics tools). For example, the average time to integrate Shipium with enterprise WMS systems like Manhattan via our APIs is ~2 months (including tuning to unique business workflows and processes).
This level of interoperability powers some advanced, impactful use cases that can help you transform shipping operations rather than just manage them.
Powerful use cases made possible by cloud-based solutions
Legacy on-premise solutions offer limited updates and expansion to new capabilities, as updates are focused on minor improvements, elimination of technical debt, and maintenance at this stage.
By contrast, the ease of integration, data leverage, and simplified process management offered by cloud-based logistics solutions give you unprecedented control over your shipping network — enabling you to rapidly adapt to changing conditions, take advantage of opportunities to lower costs, and improve efficiency throughout every stage of the process.
Let’s take a look at some of the specific use cases that cloud-based solutions can power.
Real-time delivery promise
The delivery promise you make to a customer should be rooted in data, accounting for the wide range of variables that actually impact time-in-transit. Some of these variables include:
- Historical timelines and performance for deliveries associated with specific SKUs, geographies, nodes etc.
- Order details including SKU, destination, and availability of inventory.
- Carrier performance data that can provide a reference point for how long it’s taken similar orders to be delivered by a specific carrier in the past.
- Macro-conditional data that impacts delivery timelines such as weather, labor shortages, economic conditions, and seasonal factors.
When you fail to account for these variables, you risk missing expected delivery dates, which negatively impacts customer experience and LTV. Even if your on-time delivery rate is where you’d like it to be, there’s a good chance that your margins would be stronger if you accounted and planned for these factors.
Shipping network simulation
Network simulation provides the ultimate data leverage for your shipping operations by enabling you to assess the impact of potential changes before making them. By utilizing the data that exists within your platform as well as any additional relevant data that you upload, you can run various scenarios to determine the impact of changes to carriers, service areas, rates, and just about any other aspect of your supply chain.
It’s worth mentioning that while there are point solutions built for this, the right end-to-end platform will provide this functionality natively, enabling you to aggregate and analyze relevant data in one place.
Intelligent carrier downgrades
Leveraging the Dynamic Time-in-Transit (TNT) values that we described above can also help to significantly reduce carrier costs. In fact, multiple enterprise retailers use Shipium for intelligent downgrades from premium to economy shipping options under specific circumstances, without impacting the promised delivery dates.
By accounting for carrier-by-carrier performance and other factors like current inventory levels and local infrastructure status, you can leverage predictive analytics within your shipping platform to establish a reliable SLA for economy options. With dynamic TNT values at hand, you can quickly identify opportunities to downgrade categories of shipments from premium to economy services without compromising on your delivery promise.
Packaging optimization
Packaging optimization can quickly drive down shipping costs and improve efficiency by helping you to minimize the "air" in each package, load your trucks to full capacity, enhance warehouse space utilization and streamline processes ranging from storage to packing, and minimize the risk of product damage.
You can leverage a modern solution, like Shipium’s Packaging Planner API, to automatically assign the optimal package for each shipment and consolidate order items in a way that reduces splits.
Rapid network changes
Cloud-based solutions also typically provide network management capabilities, giving operators the ability to make changes as-needed in the event of carrier disruptions, unusual weather conditions, or unexpected cost changes (ex. Increased accessorials due to higher gas prices).
Ideally, a solution like the Shipium Console will give your team the ability to make service changes, reroute inventory, optimize packaging, and much more. Greater adaptability in your supply chain will enable you to keep costs down while continuing to deliver for your customers.
Wrapping up
Cloud-based supply chain platforms represent the future of logistics technology, enabling enterprise retailers to improve performance while lowering shipping costs through a combination of data leverage, flexibility, and ease of management.
If you’re looking to modernize your logistics technology and invest in a comprehensive platform, schedule a call with our team of experts to discuss your use case.
.png)
Read Anurag Allena's Shipium blogs. Anurag is a Senior Product Marketing Lead at Shipium and an experienced software marketing professional.