How SAP EWM Optimizes Your Supply Chain
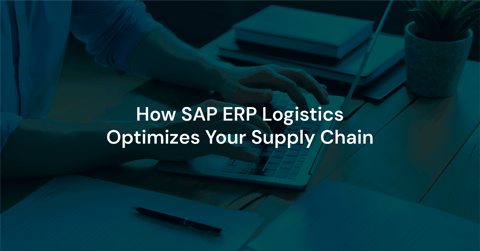
For most ecommerce businesses, supply chain management — the process that oversees a product’s journey from production to customer — is one of their most critical operational components. The SAP Extended Warehouse Management (SAP EWM) system handles order fulfillment, which is an important step in this process. But is your system correctly configured to improve your overall logistics network?
Let's break down seven ways to optimize your supply chain using SAP EWM, reducing shipping costs and streamlining your operations.
1. Expand your carrier mix
Providing a customer experience that promotes brand loyalty requires your ecommerce business to meet current consumer demands. With Amazon Prime setting the bar for delivery expectations, attempting to stay competitive with only one or two parcel carriers is unrealistic and expensive. Diversifying your shipping providers adds agility to your process, enhancing your performance.
An expanded carrier mix offers:
- Reduced shipping expenses: Using a multi-carrier strategy allows you to compare costs from different carriers to find the best rates.
- Enhanced delivery planning: Selecting from a large network of carriers allows you to intelligently route your packages based on factors like package size and carrier data.
- De-risked network: Leveraging a diverse mix of parcel carriers ensures you always have a backup plan for volume-based delays, extreme weather, or other factors affecting your delivery times.
Integrating your SAP Extended Warehouse Management system with multi-carrier shipping software like Shipium simplifies the process with a pre-integrated carrier network. The built-in network reduces the complexity of the integration process, allowing you to add carriers to your mix within a day without extensive IT or vendor intervention.
2. Implement regional logistics
While working with larger national carriers increases the reliability and coverage of your ecommerce shipping operations, enterprise-scale businesses realize cost savings and reduced time in transit by integrating regional carriers into their network that cater to smaller service areas.
Refined for specific geographies, regional parcel carriers:
- Minimize the risk of damage: Regional parcel services have more direct routes with fewer touchpoints, which helps reduce the chances of your packages getting damaged or lost before they reach your customers.
- Reduce delivery times: Local expertise within smaller service areas means regional carriers already have streamlined routes, shortening time-in-transit.
- Lower transportation costs: Proximity to your customers makes local deliveries more cost-effective, minimizing carrier rates and eliminating excessive accessorial charges.
3. Leverage fully loaded rate shopping
Ensuring that each shipment leaves your warehouse at the best rate possible is challenging. The process requires your shipping platform to connect with carrier APIs to retrieve rates. Using this information, you can implement rate shopping logic within SAP EWM to select the cheapest option.
When calculating the total cost for each shipment, you need to account for various charges, which vary from carrier to carrier.
These charges broadly fall into the following categories:
Type of charges |
Definition of the charges |
Rates |
Agreed-upon price for shipping, based on factors like origin, destination, package size, and weight |
Accessorial fees |
Additional charges for extra services, such as signature requirements or address corrections |
Surcharges |
Predictable extra costs that vary by carrier, like fuel charges. Multiple surcharges may apply to a single shipment |
A significant issue is that APIs generally don't add accessorial fees or surcharges to the rates they return, meaning when comparing costs, you may not be comparing the actual cost of shipments.
Implementing rate comparison within your EWM system, in conjunction with Shipium’s carrier management capabilities, simplifies the task of maintaining accuracy by virtualizing carrier contracts, updating weekly surcharges, and factoring in all properties for your network. With Shipium carrier selection, you get the lowest actual cost every time.
Explore how fully loaded rate shopping ensures maximum cost savings.
4. Refine your delivery promise
Today's customers expect faster shipping than ever before. A Baymard Institute survey revealed that 23% of consumers abandoned checkouts due to slower-than-expected delivery times. Providing every shopper with a fast estimated delivery date (EDD) upfront is the essence of a robust delivery promise. However, this only works if your SAP supply chain can give accurate estimates.
Without a proper system that considers all the necessary factors in your supply chain, you risk making promises you can’t keep. False promises result in premium shipping rates to meet EDD obligations and a loss of customer loyalty if deliveries arrive late.
Accurate EDDs require you to analyze:
- Network criteria: Consider components specific to your network, including distribution centers, operating schedules, carrier arrangements, and shipping preferences.
- Real-time variables: Manage changing conditions affecting delivery performance, such as daily and seasonal patterns, plus unexpected disruptions like severe weather or supply chain issues.
- Data-driven forecasts: Gather insights from machine learning analysis of your existing transit data to predict demand fluctuations and regional shipping trends.
- Carrier performance metrics: Perform comprehensive analysis of actual carrier performance across various conditions, comparing real-world results to promised service levels.
Reliable delivery dates enhance the shopping experience and help you build customer trust. For example, augmenting your existing SAP systems with Shipium’s transit calculations to get the most accurate EDDs in the industry can help increase your average conversions by around 4%.
5. Streamline your packaging
Managing how items are analyzed and packed into the right shipping boxes or cartons is key to fine-tuning your overall SAP fulfillment process. Poorly packed shipments lead to issues like oversized boxes filled mostly with air, resulting in higher costs and wasted truck space.
By streamlining your warehouse packaging process, you:
- Maximize space and efficiency: Enhance warehouse space utilization and improve truckload efficiency, leading to fuller loads and more shipments.
- Reduce operational costs: Minimize expenses associated with excess packaging materials and lower shipping rates through proper carton selection.
- Increase profitability: Avoid excessive dimensional weight charges and storage fees while reducing the likelihood of returns due to damaged goods.
While the SAP warehouse management solution offers excellent cartonization features natively, some customers look to apply the same functionality upstream within other areas of their operations. Working with a shipping partner like Shipium can help them achieve this through microservices related to packaging.
Discover how to optimize cartonization and lower shipping costs with Shipium’s packaging planner API.
6. Unify your supply chain
Integrating all aspects of operations, from inventory to delivery, facilitates a more cohesive and efficient system. A unified approach to your supply chain allows for better coordination, improved visibility, and more effective decision-making across your entire network.
A synchronized approach to supply chain management leads to:
- Accurate stock levels: Enabling real-time inventory management across all channels allows for more precise demand forecasting and helps maintain optimal stock levels across your network.
- Standardized information flow: Adopting centralized data management with API integrations empowers you to make more accurate data-driven decisions that affect your business.
- Aligned transportation and logistics: Ensuring your order, warehouse, and transportation management systems work in unison helps you generate accurate and — more importantly — reliable delivery schedules, improving efficiency and reducing costs.
Explore how Shipium helps bridge the gap between your existing systems to improve order fulfillment.
7. Monitor and enhance your process
You need to monitor your overall performance to maintain the efficiency of your workflows. Configuring the real-time visibility of measurement services within EWM’s Warehouse Cockpit and combining them with advanced insights provided by tools like Shipium Simulation will help identify potential efficiency gains and tweak every step of your supply chain.
The Simulation offering lets you test different scenarios and strategies to understand how the changes impact your current SAP optimization and affect future planning.
How impactful can simulation be for your organization? A case study showed that a Fortune 500 retailer using the tool uncovered that it could process 42% of annual shipments differently, reducing per-package cost by $0.89 and potentially saving $29.6 million.
Improve your SAP warehouse management with Shipium
Shipium helps SAP Extended Warehouse Management customers streamline processes with an end-to-end enterprise shipping solution built for modern operators. The Shipium platform, tailored to individual environments, allows SAP users to manage their parcel carriers seamlessly, driving up to 12% annual cost savings on average for ecommerce businesses with high shipping volume.
Book a demo today to learn how integrating your SAP EWM solution with Shipium optimizes your supply chain.
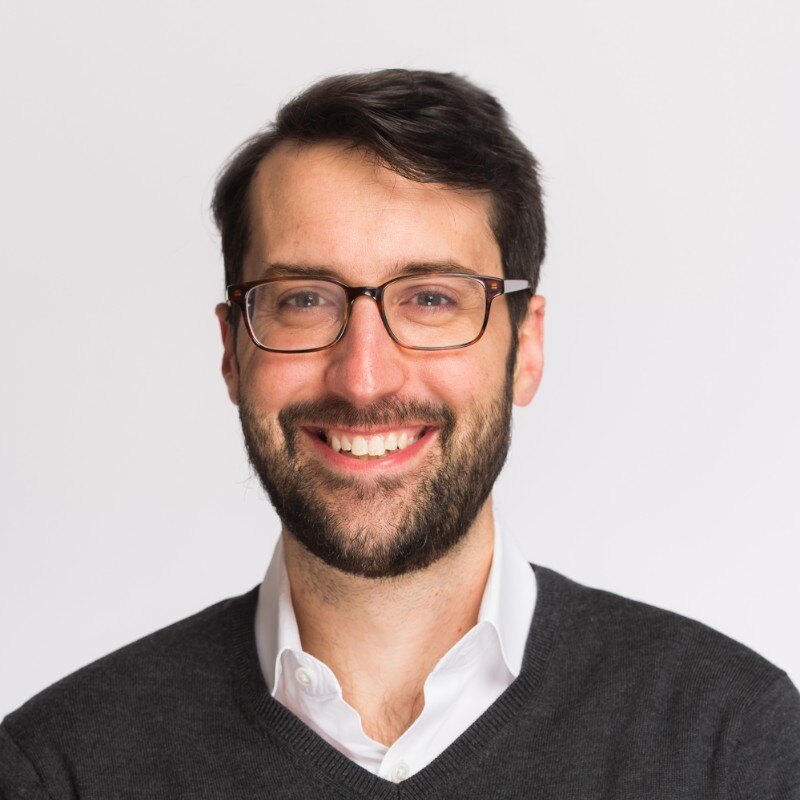
Mike leads our partnerships and alliances effort, where Shipium strives to be a world class ecosystem partner to technology providers, carriers, strategic consultants, and systems integrators.